
Humans have crafted products for millennia
It is considered that weaving, spinning, and felting are some of the oldest craft practices, most of these crafts being practised for more than 10,000 years! India’s woollen craft industry houses an amazing array of crafting practices. This industry generates rural employment opportunities at little or no cost to the environment.
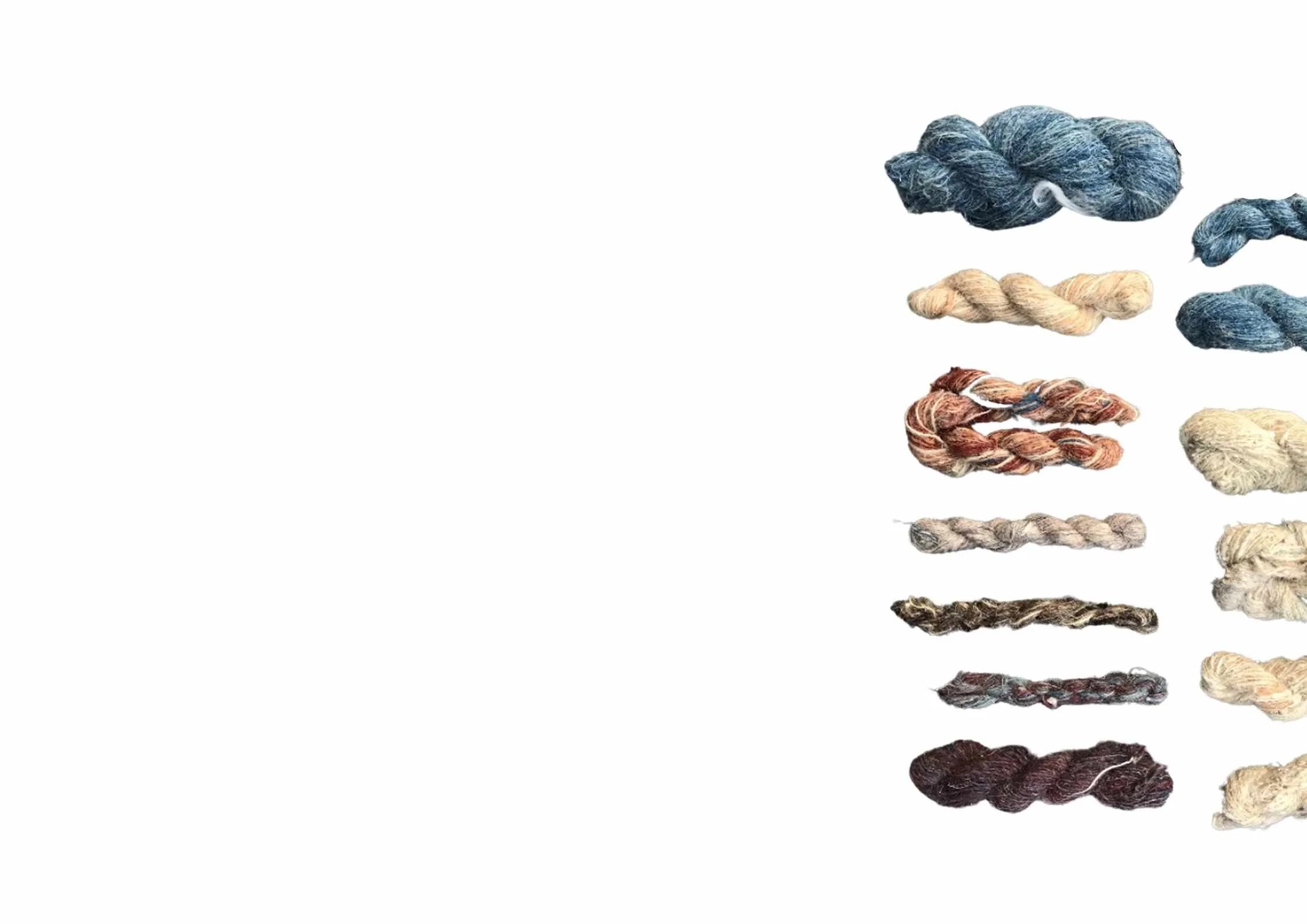
Every sheep region has its own wool-craft ecosystem. A wide diversity of colour, texture, length and width of wool fibres have shaped signature products of each region.
Ever wondered how indigenous wool is processed? It is not the same as what you see in machine-intensive wool mills. The traditional method of processing wool has a sweet slow rhythm that engages many stakeholders in the value chain.
Grooming The Fibre
-
Sheep shower
Every great piece of textile stands on the unseen foundation of pre-processing the fibre. Wool, especially, needs careful processing. And it all starts with a sound shower for the sheep! A vigorous bath washes the sheep clean and makes it easier for bands of itinerant shearers to harvest the wool. Pastoralists must shear sheep seasonally. It is crucial to sheep’s health and comfort. The unshorn wool can increase the risk for skin disease or parasites and may also impede their movement and vision.
-
Shearing
Every year before the rains and after the harvest in October, the sheep have to be sheared for their well-being. The pastoralists call for competent shearers who have the know-how and expertise in shearing the sheep without nicking, cutting or otherwise harming them. Sometimes, even when there is no market for wool or the market value of wool is insignificant, the herders still pay to shear their sheep for their animal’s health.
-
Sorting shorn raw wool
Wool is sorted and cleaned by colour and length and then handed to hand spinners. The sorting of wool is very important to obtain the best quality of fibre. This process helps remove the burr (vegetative matter) and dirt from raw wool.
-
Carding and aligning wool fibre
The spinners pluck on clumps of fibres to align them in a single direction. This arrangement is known as a puni. Puni-fication of fibres complete the pre-processing cycle. These days carding is done with carding machines.
Hand-spinning of Wool

Spinning is the art of twisting and turning fibres into yarn. The first instance of spinning is about 9,000-10,000 years old, using drop spindles. The charkha, as we know it today, began to be used widely in 500 AD. Today, most hand-spinners use a charkha. The indigenous pastoral communities in India have always spun wool.
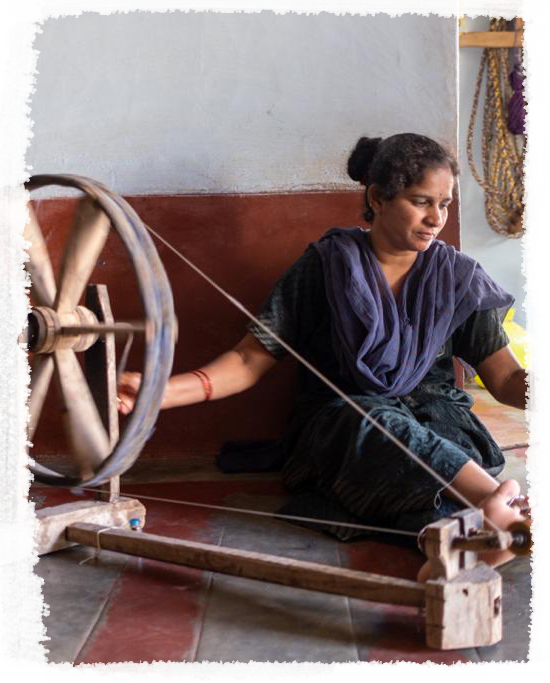
They are experts in achieving the fine balance of twist and draw to produce a variety of low/high twists and thick/thin yarn. The women use the charkha to spin. The rhythmic rotation of the charkha accompanied by the nimble draw of fibres is meditative for the spinners. The charkha has become a symbol of self-reliance for rural women as they get a chance to work from their homes and earn a livelihood.
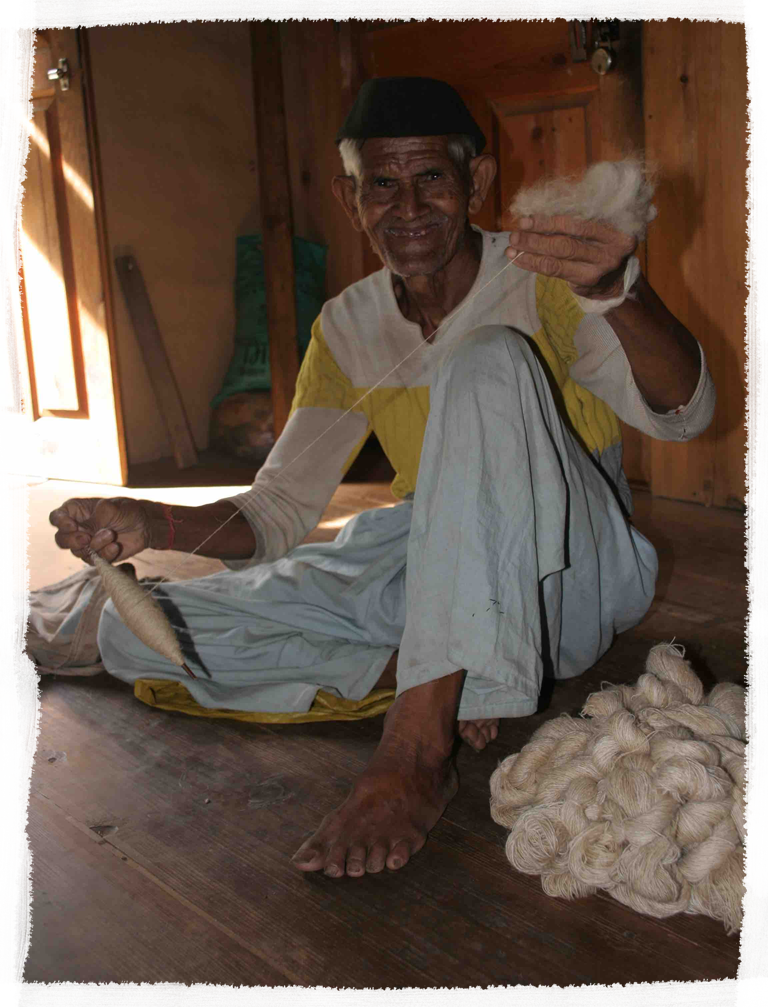
The herders also practice drop-spindle or takli spinning. Takli spinning requires no tools except a large pebble or a piece of wood lying in their path! Both sheep, yak, and camel herdsmen spin at all times; while taking it easy under a tree, ambling with the assembly of their animals, or harried hurried by headstrong ones in the herd!
Natural Dyeing of Wool

Subtle and elegant, vegetable dyes capture the sparkles of the earth like no other object. Dyes of every region present a sketch of the local vegetation, climate, and ecology.
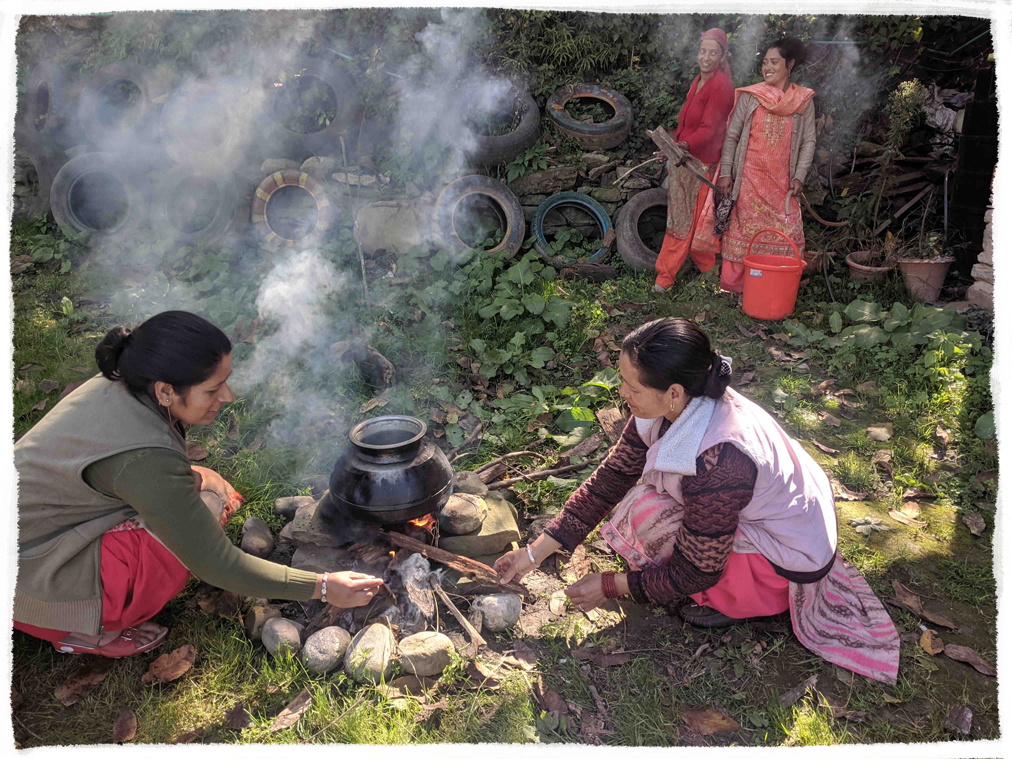
Vegetable dyeing is a test of ability as much as of endurance. Dyers have had to face many more failures than Edison to un-riddle dyeing recipes.

Wool has a special affinity for vegetable dyes. This is because the myriad reactive groups of woollen fibres are trained to capture dyes at first sight! Generally, woollen yarns are dyed with dexterity by the dyers and then handed over to the weaver.

Thankfully, today local dyers can refer to the storehouse of knowledge established by their ancestors. Many indigenous communities in India have been practising natural vegetable dyeing for centuries.
Handloom Weaving

Weaving is mystic amongst crafts. Indian saints, as well as folk culture, have often explained the non-dualities of life through the metaphor of weaving craft. Every weave establishes itself on warp threads, the taana, stretched on a loom. A textile is born when the baana, the weft, crisscrosses the taana, always so, at right angles. The weaving craft has journeyed many geographies and seen many tools, techniques, and technologies.
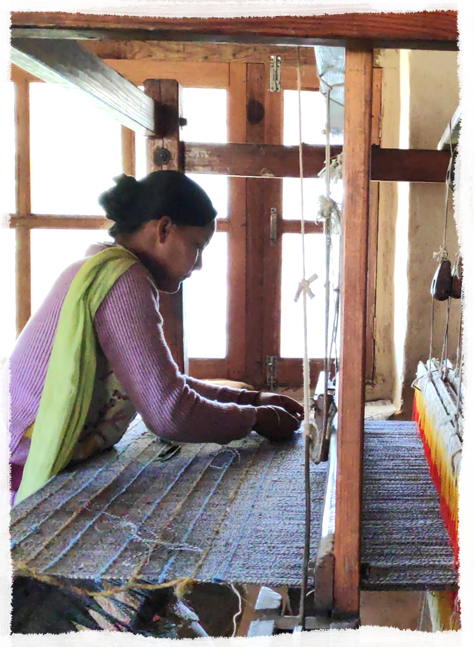
The interplay of the taana and the baana presents a sea of possibilities to a weaver and a philosopher alike. Weavers rely on tradition and their intuitive sense of balance, proportion, and harmony to navigate through this maze of possibilities. They pursue and produce without ego. Hand-spun wool is textured and fragile; its characteristics have shaped tools devised by the weavers, who have preferred softer reeds or no reeds at all!
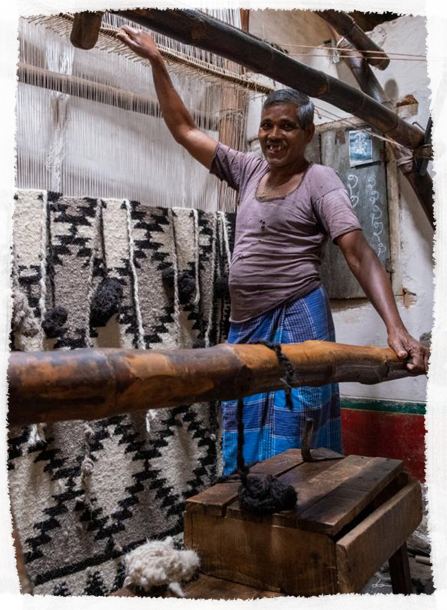
The reed made of Mojari grass is one such example. The reed is supple - it pulsates with the flow of the yarn; it wavers and wobbles; balances the twin needs of not keeping the yarn unbroken and forming a stable surface of threads. Yet another instance is the ingenious use of a coat of Varath, a wild tuber of the onion family, extracted on warp threads – it lends strength to the yarn as well as powers to fight moths that tend to feed on wool.
Hand-Knitting
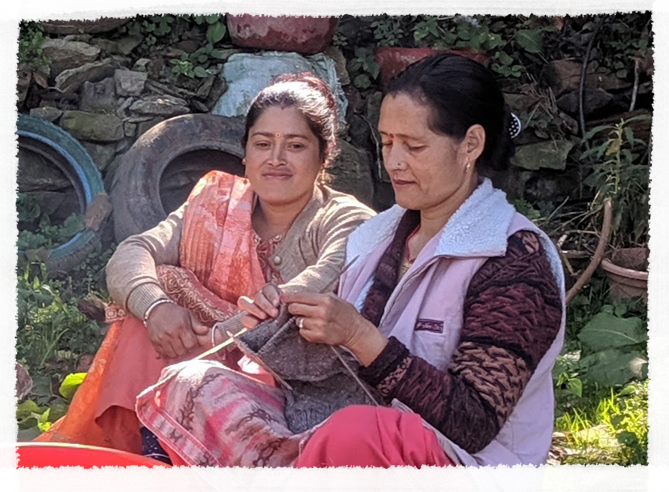
The Himalayas are also home to many knitters, a relatively new craft community.

Though not a traditional craft practice, the knit craftswomen are known to be super dexterous.
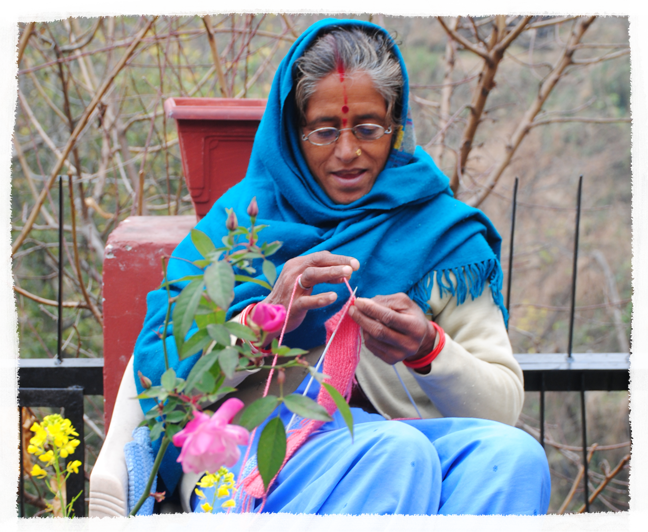
It is not uncommon to find women knitting on the move; they negotiate twisting trails and intricate designs at the same time with equal serenity; a testament to their focus, skill, and balance.
Namda: Felt Wool Craft
Watch Gulmamadbhai, a felt artisan, at work; making an aasan. In Todiya village Kachchh, Gujarat
Felting, also known as Namda, is the most versatile of all wool-crafts. Felt from wool is known to be older than the art of spinning and weaving. Felting was majorly practised by nomadic tribes across Asia and Europe because they possessed a large herd of wool-bearing sheep and camels.
In India, felting arrived in the 11th century. During the reign of the Mughal Emperor Akbar, a man named Nubi innovated a felted covering (wool saddle) for the king's ill horse. Ever since people have been making felted textiles from the sheep wool.
Tabaria Wana & Split Ply: Wool-Craft
Tabaria wana is made with sheep and camel hair yarn. The pastoralists hand-spin the yarn via takli-spinning. The weaving of Tabaria-wana is set up solely using the body as a loom, no other external tool is used to create Tabaria-wana. This was originally used by pastoralists to cover a camel's udder.
Camel girths were extensively made and used throughout the areas of western Rajasthan and the salt plains of Kachchh. These regions have had a rich pastoral culture for centuries. Pastoralists reared cows, buffaloes, camel, sheep, and goats. With hair from camels and goats, the Maldharis devised a unique braiding technique to make tangs called ply split. With ply split braiding, a plied rope is threaded in through itself.
Tangs were used to secure the many trading goods. The tang is a belt tied to one side of the wooden saddle on the camel, passes around the animal’s neck and under its tail, and is tied to the saddle on the other side. Since the wooden saddle is typically quite long, two tangs are used to secure it. The front belt is patterned, while the back belt is typically left unpatterned.

Ranabhai, a herder from Kutch shows a Tabaria Wana handwoven with camel wool. The Tabaria wana is made with sheep and camel hair yarn. The Maldharis hand-spin the yarn through takli-spinning.

The weaving of the Tabaria-wana is set up solely using the body as a loom, as each part of the body becomes tools of a loom, no other external tool is used to create a Tabaria-wana. This is used by Maldharis to cover the camel's udder.

Camel girths were extensively made and used throughout the areas of western Rajasthan and the salt plains of Kachchh. Tangs were used to secure the many trading goods.